お客様インタビュー
現場の課題解決に向けた具体的な導入事例をお客様の声と共にご紹介しております。

パナソニック株式会社 奈良工場
導入時期:2018年6月
導入地域:奈良県大和郡山市
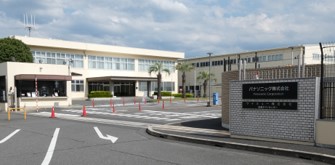
お客様紹介
パナソニック株式会社 奈良工場は1967年に暖房器、厨房器、石油機器、電子レンジの生産、1983年よりガスマイコンメータ用デバイスを生産をスタートし、現在は超音波ガスメータといった、より高精度のデバイスや自動検針といった無線デバイスなど、メータセンシング技術・無線通信技術を基盤に世界の「安心・安全」に貢献する製品を生産しています。日本のみならず欧米やアジア向け製品も拡大しています。
導入前の課題
メータデバイスのはんだ付けの自動化取り組みとしてコテロボットを導入し4~5年使用していましたが、コテ先に付着したはんだカスやワークとコテ先の距離の不揃いにより不良が発生するため修正が必要になったり、部品によっては廃棄となっていました。そのためコテ先を2時間に1回の頻度でメンテナンスする必要があり、その度に5~10分の装置稼働ロスが発生。また月一回の頻度でコテ先の交換していたため、装置の稼働ロスに加えて、メンテナンス工数ロスが課題でした。
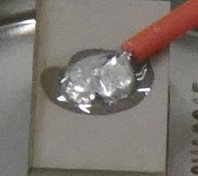
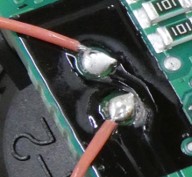
レーザはんだ付け装置(コンパクト接合レーザ)の導入決定
コテロボットの稼働ロスやメンテナンスコスト低減のため、非接触のはんだ付け工法としてレーザはんだ付け装置の導入を検討しようということになりました。レーザはんだ付け装置の選定においては数社比較検討した中で、温度監視が可能な点やパナソニックグループ内の調達しやすさなどからコンパクト接合レーザの導入を決定しました。導入にあたっては、製品の性質上10年保証を必要とする製品にこれまでやったことがない工法を採用することへの不安の声が上がり、そういった不安を払拭するための信頼性試験や保証できるスペックを確保して積み上げて管理していくことに苦心しました。特に日々の管理をどうしていくかは悩んだところですが、コンパクト接合レーザの温度監視機能はデバイスが過熱されていないかを管理する上で有効な機能でした。
導入後の変化
レーザはんだ付け装置(コンパクト接合レーザ)導入後はコテ先に付着したはんだカスやワークとコテ先の距離の不揃いにより発生していた不良が1/10に低減され、コテ先メンテナンスによる装置稼働ロスは数百分の一に低減されメンテナンスによる作業者の負担が劇的に低減されました。レーザはんだ付け装置(コンパクト接合レーザ)を導入してからはほとんどメンテナンスすることがなく、定期的に鏡筒のカバーガラスの清掃をするようにしていますが、汚れが少ないため感覚的にはメンテナンスフリーの様な感じです。
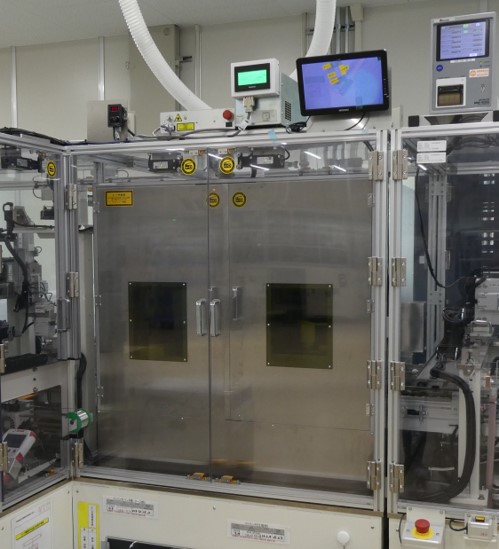
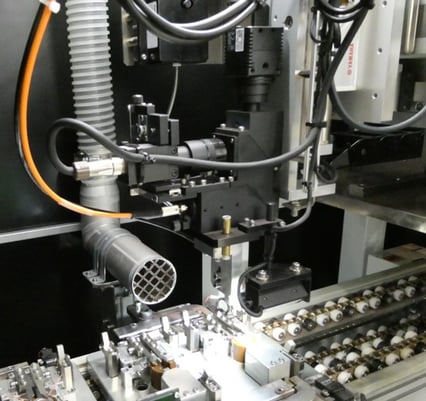

今後の展望
これまで7台のレーザはんだ付け装置(コンパクト接合レーザ)を導入していますが、海外の需要拡大のため現在フル生産状態が続いており、24年度に生産能力アップのために新たにラインの増設を計画しています。コンパクト接合レーザへの要望として、はんだ送り装置の高速化と現行の電流値によるレーザ出力設定を、誰でも分かりやすい温度による設定に進化することを期待しています。
導入検討中の方へアドバイス
ぜひレーザをやろう!最初は不安もあり、導入までは苦労もありましたが、導入後のメリットはそれを上回るものがあります。