現場の課題解決に向けた具体的な導入事例をお客様の声と共にご紹介しております。
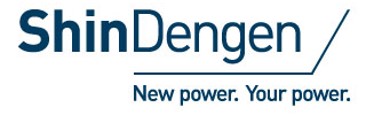
新電元工業株式会社
導入時期:2022年9月
導入地域:埼玉県深谷市
(株式会社 岡部新電元様)
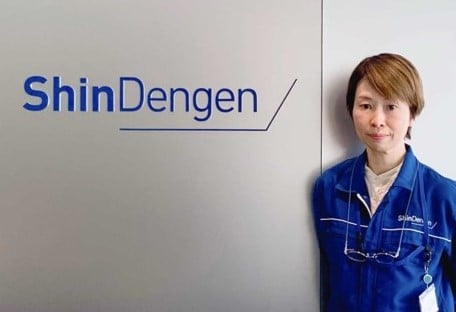
新電元工業株式会社 電装事業本部 電装事業部
生産技術部 生産基礎技術課
中村 様
導入前の課題
これまではコテロボットで生産していましたが、製品がコンパクトになり実装密度が高くなったことで、基板にコテはんだ用のデッドスペースが確保できず、コテロボットでの生産が難しくなってきました。さらにコテロボットは生産を続けているとコテ先が摩耗し、クリーニングや、1週間に1回程度コテ先の交換といった定期的なメンテナンスが必要なため、交換の度に設備稼働ロスを生じていました。
レーザはんだ付け装置(コンパクト接合レーザ)の導入決定
レーザはんだ付け装置を導入するにあたっては、コテロボットで量産している製品で、他社を含めて3社を検討していました。
その中で最もはんだ付けの出来栄えを満たしている点と、何より基板に対して直上からレーザ照射できる点が、パナソニックに決定した理由です。他社は反射による戻り光対策としてレーザヘッドを傾けて照射するため、加工点周辺の部品との干渉リスクがありましたが、直上照射はそのリスクが軽減されるため、デッドスペースの制約が少なくなることがメリットです。
付帯機能やユーザインタフェースといった点でも優れている上に、直上照射というレーザ加工の基本機能が優れていることが最も重要なポイントでした。
導入後の変化
レーザはんだ付け装置(コンパクト接合レーザ)導入後は、デッドスペースの制約が少なく、非接触のはんだ付けになったことで定期的なメンテナンスによる稼働ロスが非常に少なくなりました。
また、サイズが小さいピン(熱容量が小さい箇所)は、レーザの高エネルギー密度の効果ではんだ付けサイクルタイムが上がり、生産性がアップしています。ただ、従来のはんだ付けの感覚とは異なり、レーザの反射光の取り扱いに気を付ける必要があり、例えば熱容量が大きいピンはレーザの反射光によりレジスト焦げが懸念されるため、反射光を考慮した使いこなしを習得する必要があると考えています。

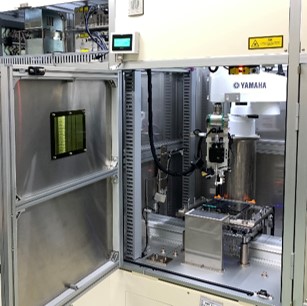
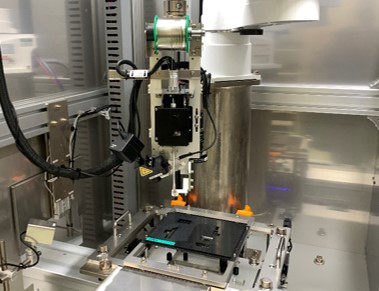
今後の展望
レーザはんだ付け装置は生産性向上、品質の安定化など導入メリットが大きいため、新製品を開発するタイミングで国内工場へ導入、さらに今後は海外の二輪向け生産工場も視野に入れて横展開していきたいと考えています。導入検討中の方へアドバイス
レーザはんだ付け工法はこれからも進化する技術だと思いますので、工法の特徴や使いこなしのコツを習得し、他社に先駆けて導入することが、今後の生産性や品質の向上に活きてくると思います。
お客様紹介
新電元工業様は1949年に設立され、売上高約1000億円、連結従業員数約5400名、主な事業は車載向けパワー半導体、電装製品、電源装置を製造されている会社様です。売上に占めるパワー半導体の比率は40%、電装製品の比率は50%。電装事業のうち、二輪車向けが80%と、特に東南アジアやインド向けの売上が拡大しています。事業の特徴として、ユニット開発する際にお客様のご要望に合わせて自社で半導体開発を手掛けることができるため、お客様の仕様に柔軟に対応されています。
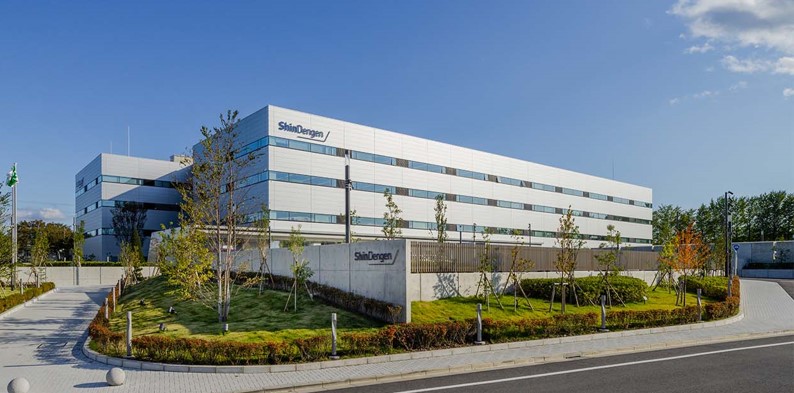
納入機器
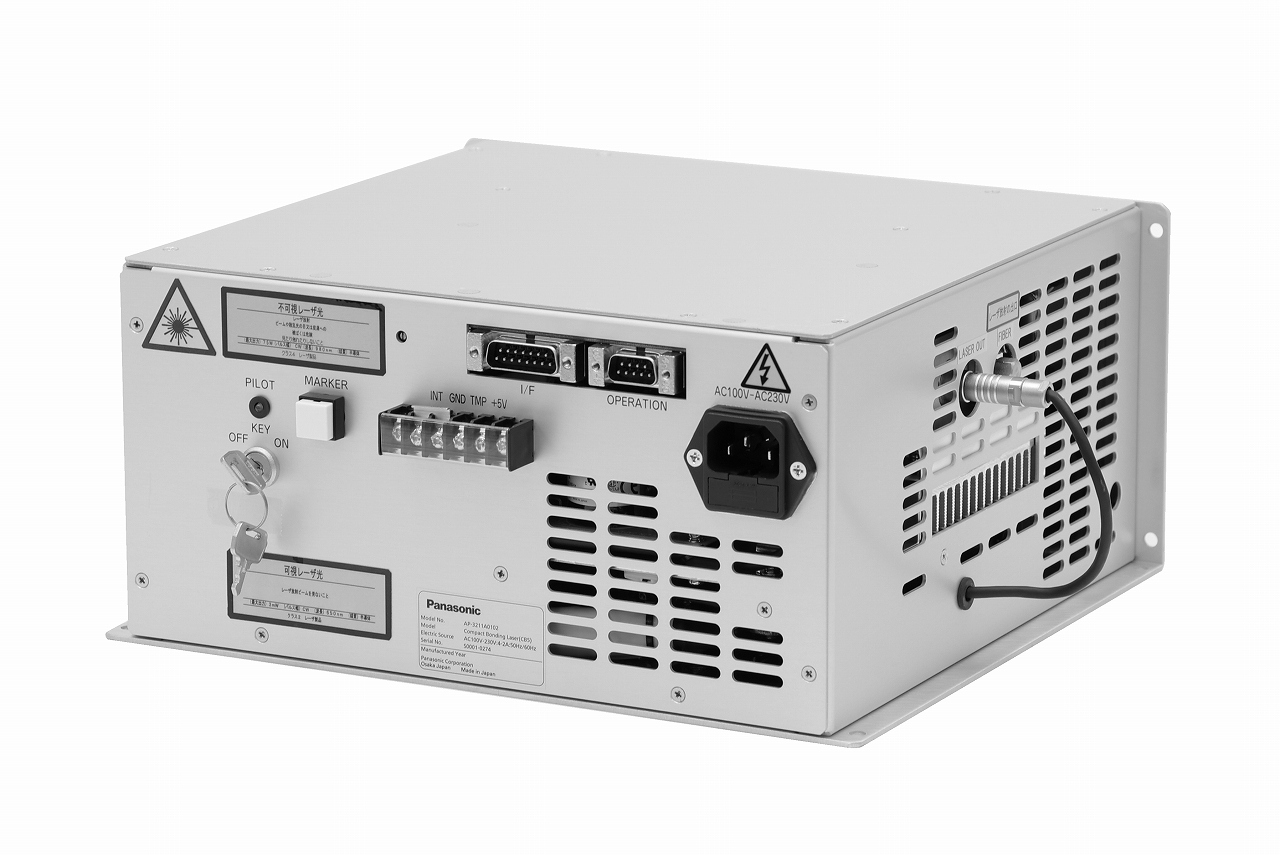
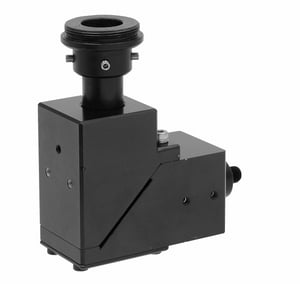
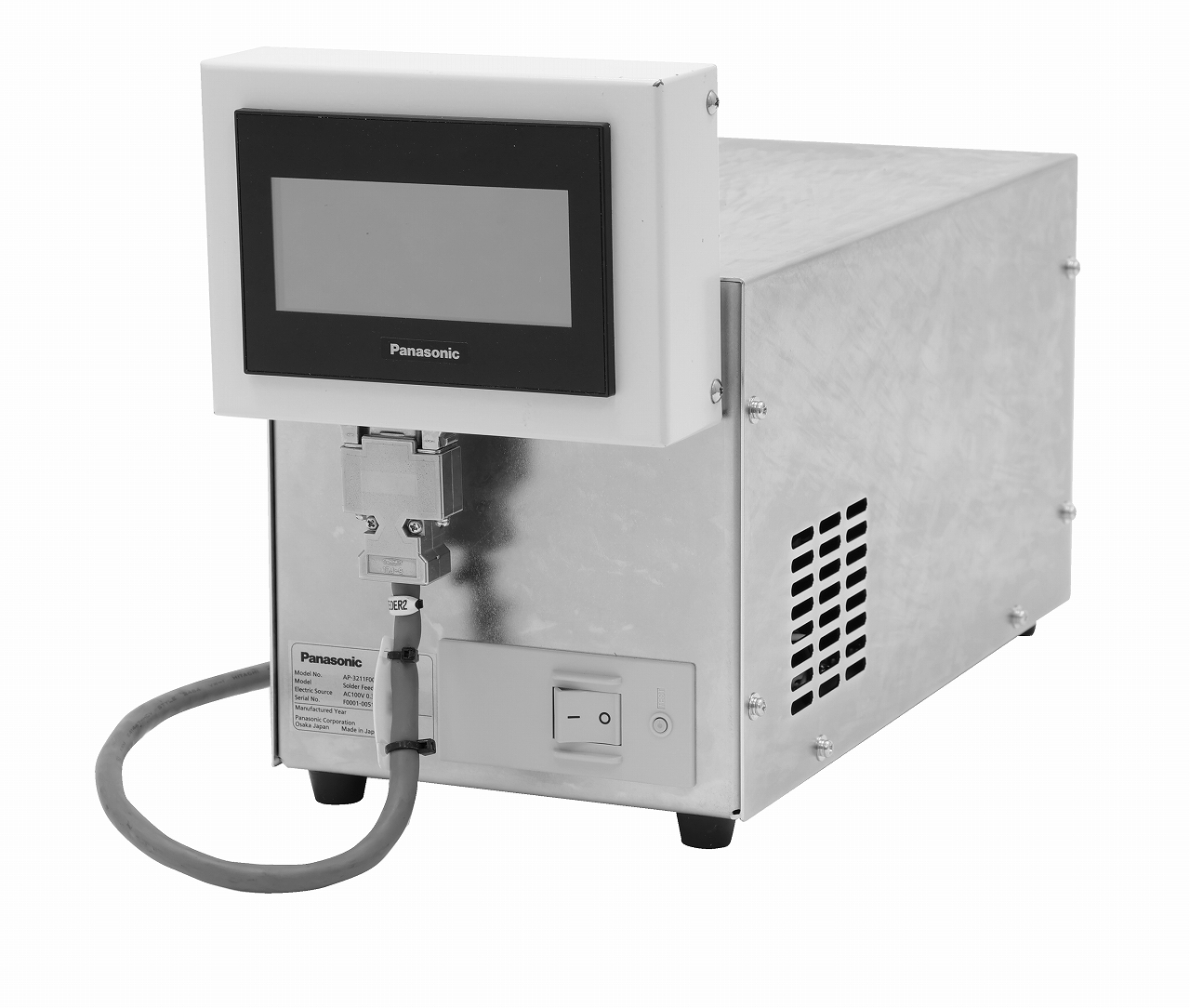